Operacje magazynowe: optymalizacja procesu kompletacji
- Analiza ABC
- Wybór właściwej metodologii pobierania
- Wybór na żądanie / Wybór indywidualny
- Kompleksowy wybór
- Wybór strefy
- Sprzęt falowy
- Skanery kodów kreskowych
- Notebooki
- Wybór głosu
Twój konsultant: Andrey Khvostikov +7 495 785 7228 Zadaj pytanie
Zapytaj eksperta
Operacje magazynowe: optymalizacja procesu kompletacji
Aby skutecznie zoptymalizować proces kompletacji, kierownik magazynu musi opracować optymalną strategię automatyzacji, która uwzględnia rodzaj przetwarzanych produktów (palety, pudła, towary drobnicowe itp.).
19.06.2018
19.06.2018
ANT Technologies
Integrator systemu przy opracowywaniu i wdrażaniu systemu WMS Logistics Vision Suite
127422
Rosja
Mlskva
ul. Timiryazevskaya, 1, bld. 2, biuro 2148-2150
+7 (495) 785-72-28
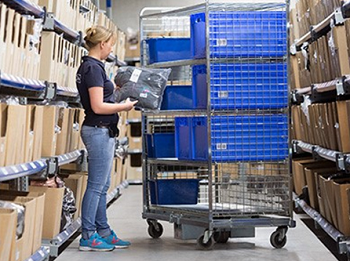
Optymalizacja procesów magazynowych wymaga podejścia wielostronnego. Podczas optymalizacji procesu kompletacji należy wziąć pod uwagę dwa składniki. Po pierwsze, żadna strategia ani technologia nie jest uniwersalna i odpowiednia dla każdego konkretnego przypadku. Po drugie, aby skutecznie zoptymalizować operacje magazynowe, konieczne jest połączenie kilku narzędzi, w tym gromadzenie danych, doskonalenie procesów i nowoczesne technologie.
Praktyczne doświadczenie pokazuje, że proces automatyzacja magazynu a wprowadzenie technologii magazynowych musi być poprzedzone procesem przygotowawczym, który obejmuje analizę ABC, odpowiednią dokumentację i analizę bieżących procesów w celu zidentyfikowania złej jakości i dalszej poprawy operacji magazynowych.
Aby skutecznie zoptymalizować proces kompletacji, kierownik magazynu musi opracować optymalną strategię automatyzacji, która uwzględnia rodzaj przetwarzanych produktów (palety, pudła, towary drobnicowe itp.).
Rozważ kroki niezbędne do optymalizacji procesu kompletacji w magazynie:
Analiza ABC
Pierwszym zalecanym krokiem do oceny skuteczności zarządzania zapasami jest zbieranie danych. Jednym z najlepszych sposobów na to jest przeprowadzenie analizy ABC w zakresie produktów.
Analiza ABC pozwala sklasyfikować ładunek w trzech kategoriach w zależności od wielkości i częstotliwości zamówień. Zadaniem jest dystrybucja zapasów zgodnie ze stopą obrotu, tj. towary o wysokim wskaźniku obrotu (A) są umieszczane bliżej strefy wysyłki, towary o niskiej prędkości (C) znajdują się dalej od strefy wysyłki. W rezultacie mniej czasu spędza się na ruchu pracownika i skraca czas pracy przy montażu towarów.
Po analizie produkt o wysokim obrocie (strefa czerwona) został przeniesiony do bardziej dostępnych stref, w magazynach zorganizowano przechowywanie mniej wymagających towarów (strefa zielona).
Wybór właściwej metodologii pobierania
Kiedy wybieramy metodę optymalizacji konfiguracji, stajemy przed koniecznością zorganizowania najbardziej optymalnego sposobu organizacji procesu. Podczas wykonywania większości operacji stosuje się podejście „selekcji na żądanie” (jedna z najbardziej nieefektywnych metod), istnieją techniki, których wprowadzenie znacznie zwiększa skuteczność doboru towarów w magazynie.
Głównym zadaniem w tym przypadku jest zorganizowanie procesu w taki sposób, aby skrócić drogę zbieracza podczas omijania obszarów składowania towarów i wyeliminować niepotrzebne ruchy.
Istnieją dwa schematy konfiguracji - „osoba na produkt” i „produkt na osobę”. System „produkt do osoby” jest opłacalny tylko dzięki pełnej automatyzacji procesów układania i selekcji towarów. W schemacie „osoba na produkt” połowa czasu próbnika jest wydawana na przemieszczanie się między adresami odbioru, 20% czasu to wymuszony przestój (czekanie), 20% pracuje z dokumentami, 10% to wycofanie towarów z miejsca odbioru. Optymalizacja pakietów ma na celu ograniczenie przestojów i ruchu.
W zależności od organizacji procesu, okres przemieszczania chwytaka między strefami montażu może wynosić do 50% całkowitego czasu montażu towarów.
Schemat „człowiek do produktu” opiera się na fakcie, że na podstawie zamówienia (lub części zamówienia) komisjoner porusza się po magazynie i zbiera niezbędne przedmioty. Po zakończeniu montażu niezbędnych towarów zamówienie jest dostarczane do strefy pakowania i wysyłki.
Rozważ najpopularniejsze metody wdrażania schematu „osoba do produktu” używanego obecnie w magazynach:
Wybór na żądanie / Wybór indywidualny
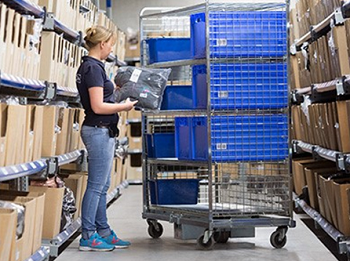
W indywidualnym wyborze komisjoner jest odpowiedzialny za montaż wszystkich elementów zamówienia. Dzięki szczegółowej liście towarów niezbędnych do montażu pracownik przemieszcza się przez magazyn i zbiera zamówienie w całości.
Takie podejście będzie skuteczne tylko w przypadku zamówień składających się z małej listy wyboru produktów. Zamówienia są przetwarzane kolejno, dokładność montażu jest wystarczająco wysoka, potrzeba przetwarzania towarów jest minimalna, wybrany produkt natychmiast pochodzi z magazynu do obszaru wysyłki.
Wadą tej metody jest niska wydajność i dokładność montażu dla zamówień składających się z dużej liczby pozycji. Wraz ze wzrostem nazw w kolejności wzrasta liczba błędów.
Kompleksowy wybór
Wydajność wyboru złożonego jest wyższa niż indywidualna selekcja, ponieważ w tym przypadku grupa zbieraczy zbiera kilka zamówień.
System informatyczny generuje listę wyboru dla kolektora, która wskazuje najbardziej optymalną trasę dla jednoczesnego wyboru kilku zamówień.
Jeśli w pierwszej kolejności musisz zebrać wszystkie zamówienia, system WMS obsługujący funkcję wyboru złożonego wskaże priorytet gromadzenia określonych elementów.
Wybór strefy
W konfiguracji strefy magazyn jest podzielony na kilka stref, z których każda jest przypisana do oddzielnego kolektora.
Podczas kompletacji zamówienia można przenosić z jednej strefy do drugiej w pudełkach, wózkach, paletach, przenośnikach itp. Jeśli zamówienie składa się z pewnej liczby pozycji towarowych w różnych strefach, wówczas dla każdej strefy tworzony jest arkusz pobrania, który jest przypisywany do wyboru kolekcjonerowi przypisanemu do strefy.
Podział kolektorów na strefy i ich znajomość lokalizacji towarów w połączeniu z możliwością jednoczesnego złożenia kilku zamówień może znacznie zwiększyć szybkość i wydajność procesu kompletacji.
Strefy zaleca się stosować w magazynach i centrach dystrybucji, w których przetwarzana jest duża liczba produktów i zamówień.
Sprzęt falowy
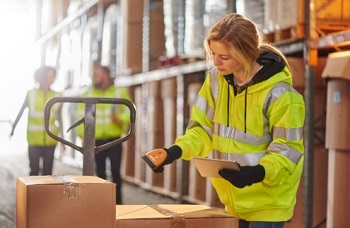
Dzięki falowej metodzie kompletacji zamówienia są grupowane i przekazywane do kolekcjonerów w zaplanowanym czasie, w zależności od czasu montażu zamówień i specyfiki magazynu.
Sprzęt Wave jest najbardziej efektywny podczas zarządzania magazynem z systemem WMS. System WMS oblicza i uruchamia kolejne fale, w zależności od konkretnych kryteriów ich formowania.
Jedną z zalet montażu falowego jest możliwość zmniejszenia obciążenia każdego kolektora, co pozwala mu skupić się na określonych zadaniach (operacjach) wybierania każdej fali.
Wdrożenie technologii: Przejrzeliśmy główne opcje optymalizacji procesu kompletacji, teraz rozważymy aspekty technologiczne
Skanery kodów kreskowych
Wdrażanie metodologii kodów kreskowych i wykorzystanie w pracy skanery kodów kreskowych to jedna z najłatwiejszych i najbardziej skutecznych opcji usprawniających operacje magazynowe. Dzięki zastosowaniu kodu kreskowego możemy skuteczniej identyfikować produkty i ich lokalizację.
Łącząc użycie skanera kodów kreskowych i listy wyboru, kolekcjoner może potwierdzić bezbłędny wybór elementów dla każdego zamówienia. Zastosowanie kodów kreskowych w magazynie umożliwia pracownikom szybsze wykonywanie operacji przy minimalnych błędach.
Notebooki
Komputery przenośne to kolejna technologia, która pozwala nam osiągnąć znaczące wyniki w optymalizacji procesów magazynowych.
Notebooki wyposażony w mały ekran i klawiaturę, dzięki której użytkownicy wchodzą w interakcję z systemem WMS w czasie rzeczywistym z dowolnego miejsca w magazynie.
Noszenie urządzenia na nadgarstku pozostawia ręce selektora wolne do wykonania niezbędnych operacji.
Dostępność wdrożenia tej technologii musi być wspierana przez funkcjonalność systemu WMS pracującego w magazynie.
Wybór głosu
Korzystanie z wybór głosu w procesie kompletacji zwiększa efektywność selekcji. Selektor, wyposażony w zestaw słuchawkowy z mikrofonem, łączy się bezprzewodowo z systemem WMS.
Podczas wykonywania kompletnego zestawu operator, używając poleceń głosowych, wchodzi w interakcję z systemem zarządzania magazynem, program z kolei przesyła dźwiękową informację o miejscu, ilość potrzebną do wyboru towarów.
Najważniejsze korzyści:
- Zwiększ dokładność i wydajność
- Zmniejszone błędy wprowadzania danych
- Wielojęzyczność
Zaawansowane technologie, takie jak Wybierz światłem , RFID, Pick-by-Vision może znacznie poprawić efektywność wyboru towarów w magazynie. Jednak wcześniej opisane technologie są bardziej przystępnymi rozwiązaniami, które przynoszą wymierne rezultaty.
I wreszcie, ważne jest, aby zrozumieć, że głównym czynnikiem optymalizacji procesów magazynowych jest możliwość gromadzenia i analizowania danych, ulepszanie obecnych procesów, wprowadzanie odpowiednich technologii w „słabych” miejscach.
Jeśli potrzebujesz dodatkowych informacji na temat usprawnienia procesów magazynowych, skontaktuj się z naszymi specjalistami pod numerem telefonu 8 (495) 785-7228 lub e-mailem [email protected]